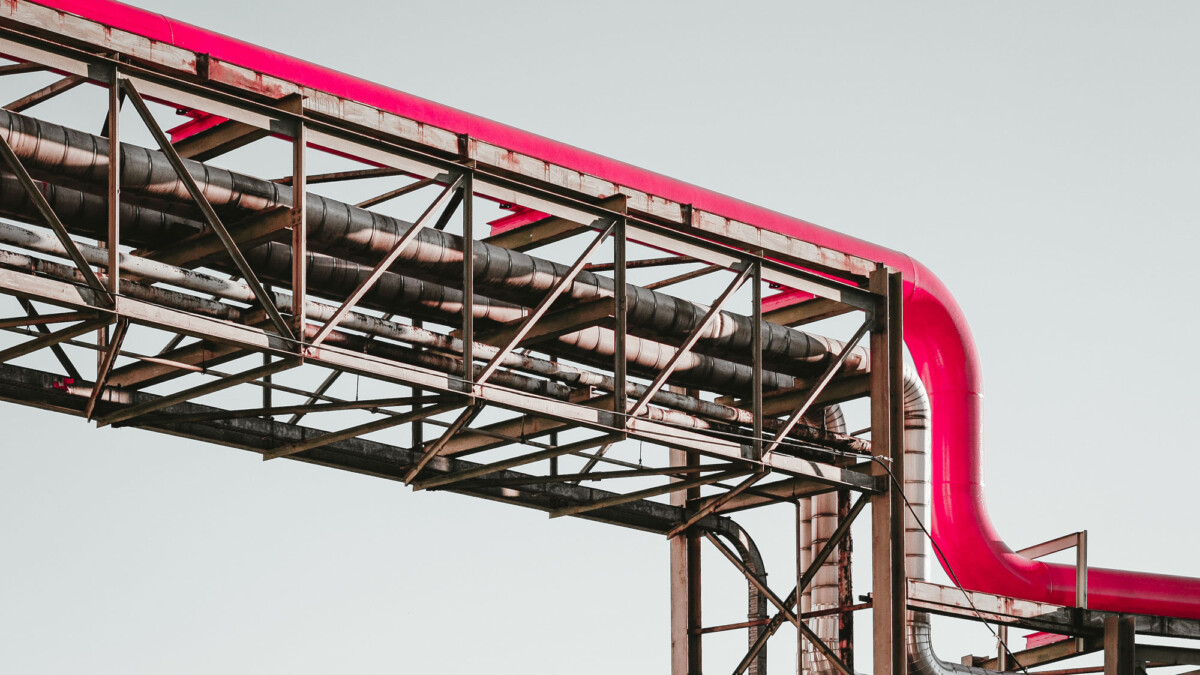
Denken Sie klein!
ZEIT RedaktionDas Schlagwort „Industrie 4.0“ feiert Zehnjähriges, aber der Mittelstand ist eher ernüchtert. Dabei gibt es ein Erfolgsrezept, das manche Unternehmer vor lauter Buzzwords leicht übersehen.
Redaktioneller Beitrag aus: „ZEIT für Unternehmer Ausgabe 4/2023. Geschäftspartner der ZEIT Verlagsgruppe haben auf die journalistischen Inhalte der ZEIT Redaktion keinerlei Einfluss.“
Es ist schon Wehmut dabei, wenn Bernd Falz von seiner Idee erzählt, die seinen Drahtwerken den Weg in die Zukunft geebnet hat – bis sie zu einem Auslaufmodell wurde. Anfang der Neunzigerjahre hat der Unternehmer selbst jene Software geschrieben, über die in seinen beiden Drahtwerken sämtliche Aufträge abgewickelt wurden, von der Bestellung bis zur Lieferung. Im vergangenen Jahr hat er die Anwendung in einem der beiden Werke abgeschaltet. Im anderen Werk soll der Wechsel auf das neue zentrale Ablauf- und Betriebsprogramm – kurz: ERP – in diesen Tagen folgen. „Die Technik entwickelt sich weiter, meine IT-Kenntnisse leider nicht mehr“, sagt Falz. Sein Bruder Holger, mit ihm in der Geschäftsführung des Familienbetriebs in Altena, hatte auf eine Modernisierung gedrängt. Eine, die mehr Zukunft verspricht.
Mehr Zukunft für ein Unternehmen mit viel Vergangenheit. Seit fast 300 Jahren wird hier im Sauerland Draht gezogen; die beiden Werke heißen Claas und Klincke, benannt nach den Familien, die 1738 und 1837 damit angefangen haben. Aber Tradition allein reicht nicht, es braucht Innovation.
Die Software von Bernd Falz erfasst nämlich nur, von welchem gigantischen Stahlring der Draht stammt. Aber sie ist blind dafür, welche Stationen er auf dem Weg von der Rolle bis zum Versand durchläuft. Mit der neuen Software wird jeder Arbeitsschritt digital erfasst, und einzelne Drähte lassen sich mittels Etikett während der Produktion nachverfolgen. Die Stationen sind nun mit industrietauglichen PC-Arbeitsplätzen ausgestattet. „Man kann so jederzeit sehen, was in den Schritten vorher passiert ist“, sagt Falz. Das ist wichtig, falls Kunden sich beschweren. Falz’ Leute können schneller herausfinden, wo Fehler in der Prozesskette entstanden sind – ob vor Ort im Draht- oder schon im Stahlwerk. „Die digitale Technik erhöht das Sicherheitsgefühl bei uns“, sagt der 62-Jährige.
Bernd Falz könnte jetzt schwärmen von der digitalen Fabrik, in die sich seine Werke verwandeln. Doch der Unternehmer neigt nicht zu Überschwang, wenn es um das IT-Projekt geht. Die grundsätzliche Entscheidung sei richtig gewesen, sagt Falz, „da gibt es keine zwei Meinungen mehr“. Aber: Drei Jahre Arbeit liegen hinter ihm, einen siebenstelligen Betrag hat seine Familienfirma investiert. Viel Geld für ein Unternehmen, das zuletzt einen Jahresumsatz von knapp 45 Millionen Euro ausgewiesen hat. Und das Zwischenergebnis? „Noch müssen die Mitarbeiter bei den neuen Abläufen viel beachten, das frisst noch Zeit“, sagt Falz.
Ernüchterung statt Euphorie: Dieses Gefühl macht sich bei vielen produzierenden Unternehmen breit, die ihren Betrieb digitaler aufstellen wollen. Dabei feiert ein großes Schlagwort gerade Jubiläum, das eine goldene Zukunft versprach: Vor zehn Jahren wurde die „Plattform Industrie 4.0“ angekündigt, ein Koordinationsgremium zwischen Politik und Wirtschaft. Hinter dem Schlagwort verbirgt sich ein hehres Ziel: Maschinen sollen miteinander vernetzt werden, ja, sie sollen sogar mit den Industriegütern kommunizieren können, die sie herstellen. Du wirst mal in der Automobilindustrie gebraucht, lieber Draht? Dann biegst du hier in Richtung einer speziellen Ummantelung ab. Und du bist ein verbogener Draht? Ab in den Ausschuss. Sensoren und Software sollen ermöglichen, was bis dahin nur Menschen vermocht hatten. Das erhoffte Ergebnis: eine schnellere, flexiblere, ressourcenschonendere Produktion – von der Bestellannahme bis zur Lieferung.
In der Praxis nutzte der Begriff zunächst Beratern und Softwareanbietern. Einige Konzerne gingen mit Leuchtturmprojekten voran. Aber dem Mittelstand selbst fehlen bis heute häufig Zeit und Geld für eine digitale Runderneuerung. In manchen Fällen wurde mit viel Elan ein erstes Projekt angeschoben, brachte am Ende aber den Betrieb kaum voran. Yvonne Therese Mertens kennt das Phänomen. Sie ist die Gründerin des Kölner Start-ups Oniq, das sich darauf spezialisiert hat, digitale Prozessabläufe in der Produktion zu etablieren. Sie sagt: „Die Firmen haben sich häufig zu viel vorgenommen – und wenn der Erfolg dann nicht eingetreten ist, war die Enttäuschung groß.“
Dabei herrscht grundsätzlich Einigkeit, dass mehr passieren muss. Eine Studie der Unternehmensberatung Staufen kam im Frühsommer zu dem Ergebnis, dass knapp 60 Prozent der befragten Firmen an Industrie-4.0-Projekten festhalten, selbst wenn sich die wirtschaftliche Situation verschlechtert hat. Das Bewusstsein ist da, dass Digitalprojekte zu weniger Kosten oder besseren Geschäften führen können. „Beim Thema Digitalisierung geht es schon lange nicht mehr um das Ob, sondern nur noch um das Wie“, bilanzieren die Autoren.
Eine zentrale Herausforderung dabei: Die Stärken von deutschen Mittelständlern und internationalen Techkonzernen passen oft nur schwer zueinander. Auf der einen Seite stehen individuelle Fertigungsverfahren und Prozesse, die über Jahrzehnte verfeinert wurden. Auf der anderen Seite Softwarelogiken, die auf Standards und schnelle Skalierung setzen. „Das sind zwei Welten, die sich nicht gut kombinieren lassen“, sagt Sven Hoffmann, Mitarbeiter im Mittelstand-Digital Zentrum Ländliche Regionen in Siegen. Es geht schon. Wenn auch häufig kleiner und unspektakulärer, als es die Vision „Industrie 4.0“ verheißen hat.
Die Firmen haben sich häufig zu viel vorgenommen – und wenn der Erfolg dann nicht eingetreten ist, war die Enttäuschung groß.
Yvonne Therese Mertens, Unternehmerin
„Wir kommen Tag für Tag ein Stückchen weiter“
Zwei Perspektiven erleichtern den Start. Zum einen der kritische Blick auf das eigene Unternehmen. „Eine Grundidee ist es, nach Zeitfressern und Fleißarbeitsaufgaben zu suchen“, sagt Hoffmann, „da kann man immer gut ansetzen.“ Je weniger ein Prozess mit dem Kerngeschäft zu tun hat, desto leichter fällt oft der Start. Bernd Falz etwa hat im Laufe der vergangenen Jahre seine Ablage digitalisiert – Dokumente finden sich jetzt per Suchleiste, nicht erst bei einem Gang in die Aktenkeller. Kein Industrie-4.0-Leuchtturmprojekt, eher triviale Digitalisierung – sie spart dem Mittelständler aber viel Zeit und Geld.
Zum anderen hilft es, wenn Unternehmer sich früh einen Überblick darüber verschaffen, was für den eigenen Betrieb Sinn macht. In einem Workshop des Fachgebiets für Produktionsorganisation und Fabrikplanung der Uni Kassel haben Unternehmer und Produktionsmitarbeiter das mithilfe eines sogenannten Reifegradmodells durchgespielt: Wo steht mein Betrieb in puncto IT und Datennutzung? Wo wollen, wo müssen wir hin? Und welche Tätigkeiten und Investitionen müssten dann aufeinander aufbauen? Es gehe nicht darum, alles sofort umzusetzen, sagt Nicolas Wittine, ein wissenschaftlicher Mitarbeiter. „Aber man sollte über alles einmal nachgedacht haben.“
Dem Unternehmer Alexander Storck aus Melsungen blieben nach dem Kasseler Workshop etwa Augmented-Reality-Brillen im Gedächtnis. Mit ihrer Hilfe könne man Mitarbeiter unterstützen, wenn sie sich einarbeiten, sagt Stock. RFID-Chips, die eine exakte Nachverfolgung von einzelnen Produkten ermöglichen, machen für den Produzenten von Beipackzetteln und Medikamentenaufklebern hingegen weniger Sinn: „Das lohnt sich nicht bei Cent-Artikeln.“
Storck will seine Firma Die Pharmadrucker mit einer neuen Software ausstatten. Das große Ziel: Auftragsinformationen sollen gänzlich automatisiert durchs Unternehmen gleiten und Maschinen sich selbsttätig melden, wenn Optimierungsbedarf besteht. „Wir haben die Daten bereits, aber wir hören noch nicht zu“, sagt Storck.
Die Schwierigkeit: Theoretisch sollten die Maschinen verschiedener Hersteller in der Druckerei über ein zentrales System miteinander kommunizieren können – in der Praxis tun sie es selten, auch weil ein einfacher Standard fehle, erklärt Storck. Doch es soll weiter vorangehen. Freitagnachmittage in Storcks Firma sind nun für Transformationsprojekte geblockt, die auch scheitern dürfen. Mit diesen Freiheiten will Storck seine 75 Mitarbeiter anregen, mehr auszuprobieren und umzusetzen.
Bernd und Holger Falz aus dem Sauerland kamen bei ihren Digitalisierungsbemühungen auch immer wieder ganz praktische Probleme in die Quere: Die Sperrung einer Autobahnbrücke verhinderte, dass eine wichtige Maschine angeliefert werden konnte. Und vor zwei Jahren beschädigte ein Hochwasser eins ihrer Werke schwer.
Doch mittlerweile wurden einige der jahrzehntealten Maschinen mit speziell geschützten Rechnern ausgestattet. Sie ermöglichen es, die Drähte zu etikettieren und auf dem Weg durch die Fabrik nachzuverfolgen. Zugleich hat Bernd Falz an zentralen Anlagen Stromzähler anbringen lassen. Sie schalten automatisch in den Schleichgang, falls das Unternehmen seine vereinbarten Stromlastspitzen überschreitet.
Dahinter verbirgt sich das eigentliche Erfolgsrezept: kleine Dinge lösen statt große Dinge denken. Nicht von Buzzwords aufscheuchen lassen. Ein Projektplan für die umfassende voll vernetzte Industrie-4.0-Modellfabrik? „Meine Gedanken kreisen eher um die alltäglichen Anforderungen im Betrieb“, sagt Falz. „Wir kommen Tag für Tag ein Stückchen weiter.“ Ob das gelingt, will er nicht an den Maschinen messen, sondern an den Menschen. „Die Mitarbeiter stöhnen längst nicht mehr so laut wie am Anfang“, sagt der Unternehmer. Und das ist mehr wert, als man vielleicht denkt.